How academic medical centers can plan like an IDN
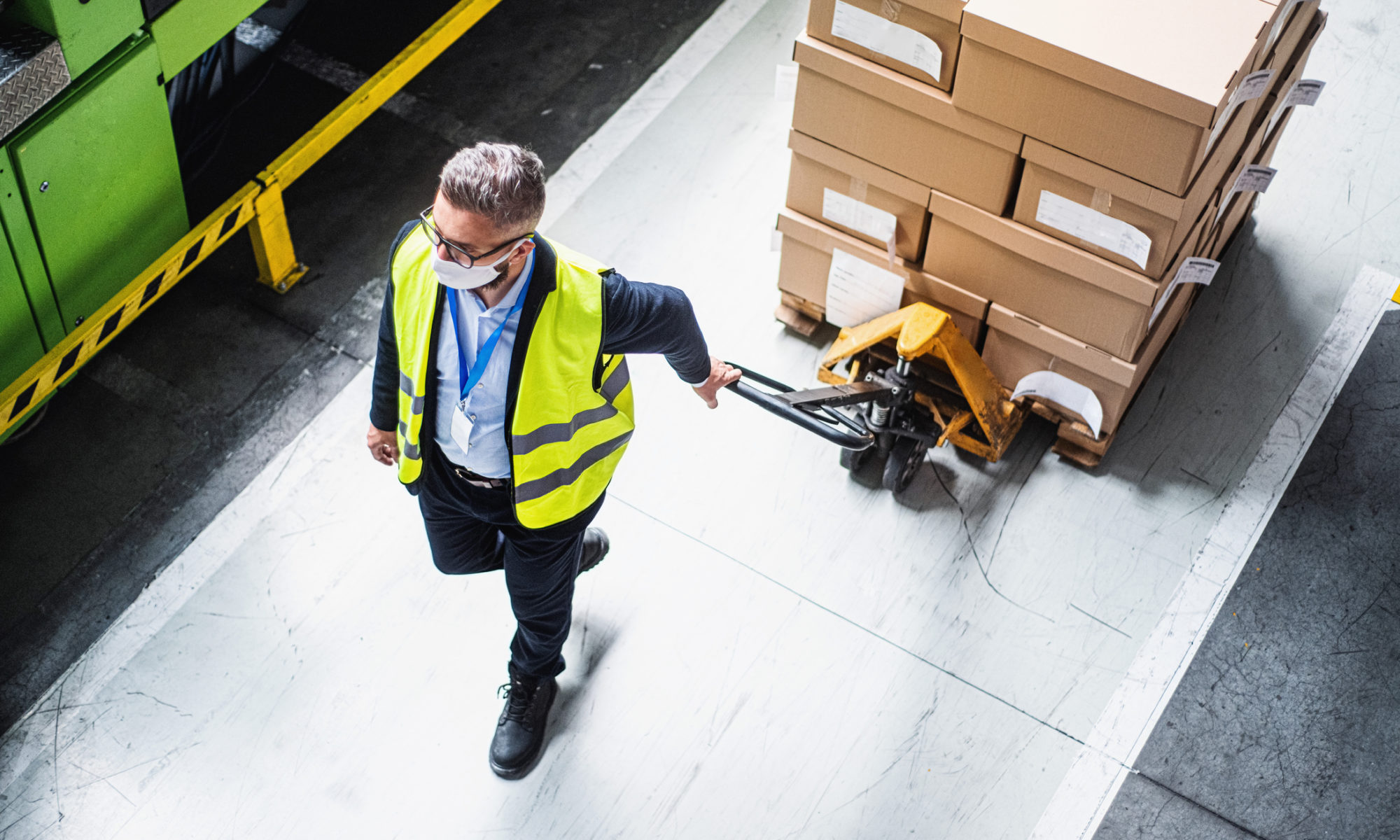
A look at how UC Davis modernized its supply chain
By Julie Alvarez | February 17, 2021
By Julie Alvarez
The University of California, Davis has weathered the pandemic better than a lot of universities, in part because of key decisions some of my colleagues made last year. That doesn’t mean there haven’t been challenges, or that the university, its hospital system and research facilities are out of the woods quite yet. Still, I believe the work we have done modernizing our supply chain has put us in a position to be closer to a hospital system in terms of efficiencies and planning than many universities. Here are some of the key takeaways of the strategies that got us where we are today:
Leadership put us on a path for success
I am a supply chain leader dedicated to life sciences. This role does not exist at many universities, even those with affiliated hospital systems and research facilities. By creating my role, the university has empowered me to spend the time necessary to build trusting relationships with my internal clients at the school and research facilities.
I’m on campus regularly, and having a face-to-face relationship with stakeholders paves the way for tough conversations when I need to have them. For example, when shortages were projected, I was able to rally life science staff to make consolidated orders in time to avoid disruption of service. As a result, the research labs were able to stay open throughout 2020, which meant that researchers could apply for key grants and secure funding during a time when many facilities had to close due to equipment and PPE shortages.
The “COVID store” made PPE available
Before COVID, it may have seemed inconsequential whether a university had a retail store on campus where staff and students could access medical and cleaning supplies. But having that final piece of the supply chain where UC Davis could warehouse and distribute products it had procured became vital once the pandemic hit. We went from ordering and storing $40,000 worth of product a year to $500,000 in a year. Students and staff had an easy way to buy (or in some cases get free) PPE and cleaning supplies. While this model may not be appropriate for all universities, schools should take a holistic look at their supply chain preparedness. One part of that may include reevaluating warehousing strategies to make sure your institution is in a position to effectively get the necessary equipment to students and staff.
Communication leads to compliance
One thing that connects my work with the folks who built our COVID-19 testing program is the idea of compliance. They made certain decisions, like making the tests quick to administer and convenient for students and staff to get them done, in order to boost compliance with the protocol. Simply making it a requirement doesn’t ensure compliance. In the same vein, saying something will be required when it comes to standardized purchasing does not mean that the message will land and that stakeholders will immediately change their behavior. Communication, specifically explaining the “why” behind the decision and sharing it with enough lead time, gives stakeholders the opportunity to share their thoughts and opinions, which can lead to getting folks on board. Labs and departments have often been able to make purchasing decisions independently in the past, so taking the time to communicate with those leaders -helped them understand the value behind any change or shift toward standardization.
There are surely challenges ahead. We are continuing to test student, staff and the community, and have begun rolling out COVID-19 vaccines. With some of the tactics I’ve outlined, we have been able to keep the campus supplied and prepared.
No single strategy will erase the threat of COVID-19 from campuses across the country, and schools should take this time to reevaluate whether their supply chain could be doing more to support their overall health goals.
If your organization isn’t set up this way already, look for ways to get departments across your university and medical center to work together. Working as one campus really helped us to protect students and staff and operate as efficiently as possible during this pandemic. We had departments willing to give inventory to others. This is a different approach than many universities with affiliated medical centers where each department operates independently. College campuses may not be used to purchasing this way, but this strategy helped build a sense of common purpose and sustainable lines of communication that have helped position Davis for success.
Subscribe to our Newsroom Newsletter to stay up-to-date on the latest news in medical supply chain.
Julie Alvarez
Senior Strategic Sourcing Manager at University of California, Davis
Alvarez is a graduate of UC Davis. She worked 17 years as a lab researcher in the agricultural biotech industry. In 2008, she pivoted her career to procurement support of industry researchers, specializing in scientific and agricultural sourcing. Alvarez joined UC Davis Procurement & Contracting Services in 2016, specializing in life sciences and medical sourcing and contracting.