The Power of Teamwork
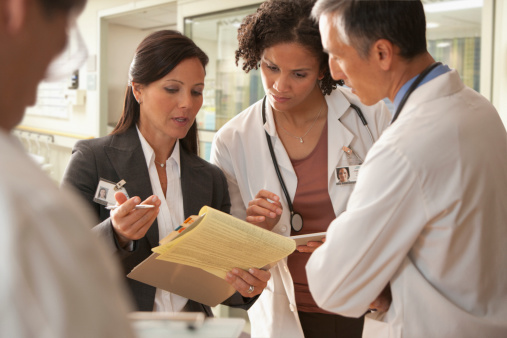
By Antonia Finlayson | March 2, 2017
Teamwork is integral for any process improvement program, such as a lean assessment, because these are the individuals whom the packs will impact significantly. However, surgery centers are a stressful environment with multiple assigned roles, and good leaders know that changes affecting day to day operations require buy-in to make it a success. In the case of the Surgery Center at Health Park in Grand Blanc, Mich., they were looking for ways to manage supplies more efficiently.
The materials coordinators at this surgery center, Amy Matney and Chari Soja, understand firsthand the importance of teamwork. They invited the entire team – nurses, technicians and surgeons – to join the discovery process. “We knew that in order for us to be successful, we needed everyone’s input from the start.”
To address these issues, Medline started with an assessment of the facility’s current needs and practices — examining its existing packs for a variety of surgical procedures and evaluating the effectiveness of its storage space.
Seeing the big picture
As much as 50 percent of the cost of surgical procedures comes from the cost of medical supplies.¹
And that doesn’t include the staff time and effort required to order, receive and store those items. Determining the optimal mix of routine, procedure-specific products allowed Medline to recommend changes that result in increasing efficiencies, streamlining supply inventory and improving storage space.
Owning the process
Matney found creative ways to start and continue the process at Health Park. No one knows the day-to-day work flow and supply needs of an ASC better than the people who work within the facility every day. That’s why getting feedback from ASC staff was critical. Following Medline’s initial assessment, the surgery center team was asked to review the new Medline-proposed program. “We set up the nonsterile packs in the conference room and invited everyone to walk through and provide their feedback,” Matney says. The feedback, combined with Medline’s analysis, enabled the Michigan ASC to implement a custom surgical pack program that was a win-win on all fronts. First, having the team review the proposed packs ensured accuracy through production. Second, it required staff members to take ownership of the program, gaining full acceptance at the time of implementation.
The bottom line: Everyone felt invested in the outcome.
The results
Here’s how the Surgery Center at Health Park benefited from its lean analysis.
- Supply protocols increased from 5 to 15
- 86,400 items were removed from its annual supply stream, resulting in a reduction of 572,000 touch points
- Surgical coverage increased from 61 percent to 97 percent
- Prep time decreased
- Fewer components were pulled
Though our reps are in constant communication ensuring day-to-day operational success, we work with our customers on a comprehensive review at least once a year. As for the Surgery Center at Health Park, almost everything their staff has implemented to improve its supply management process has been a staff effort and that’s the power of teamwork.
Click here to learn more about Medline’s lean analysis from Medline’s Outpatient Outcomes magazine and sign up to receive future issues.
Antonia Finlayson
Vice President of Marketing for Specialty Sales
Antonia Finlayson is responsible for creating marketing strategies and working with customers to find solutions for ambulatory surgery centers, physician offices, transplant organizations, research facilities and career colleges. She graduated from the University of Illinois and completed her Master’s at DePaul University. She also owns and creates content for an outpatient facilities’ magazine, Outpatient Outcomes. Prior to Medline, Finlayson was a global marketing and product manager at Thermo Fisher Scientific. She is a member of PWH, LPA, ASCA and AALAS.